The benchmark in brass and bronze casting
Marine-grade metal casting parts
When you need metal parts that hold up in marine and other harsh, wet conditions, you need a brass and bronze foundry with a broad range of in-house design, engineering, tooling and casting capabilities—plus the experience, processes and know-how to meet exacting specifications again and again.
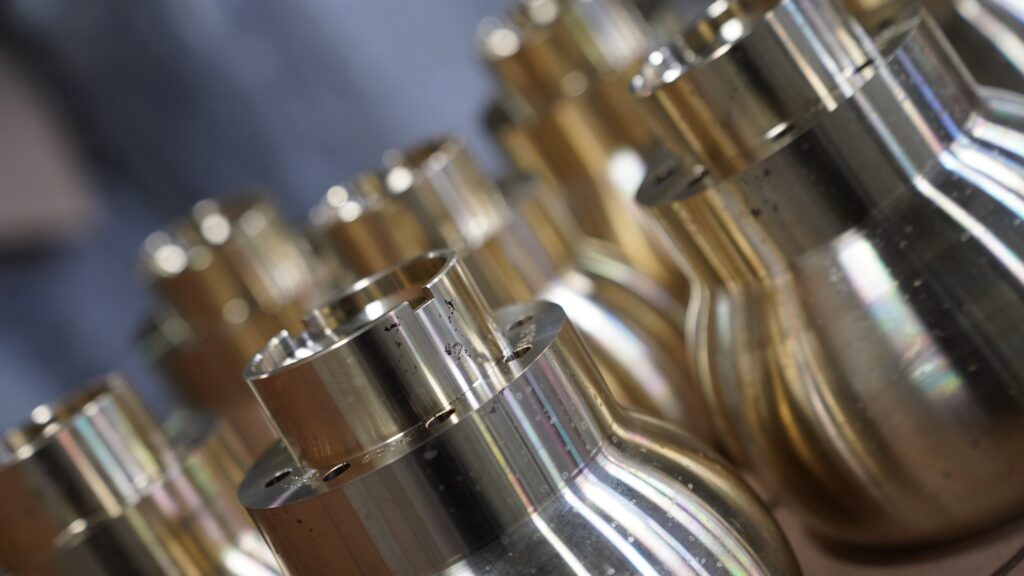
A reputation for specialty brass and bronze casting
Wisconsin Aluminum Foundry (WAF) has 115+ years of experience casting corrosion-resistant metal components. That includes brass and bronze casting. From marine applications to fire suppression systems and beyond, our engineers work with your team to meet every specification and achieve better durability—from custom brass casting to the most specialized bronze castings.
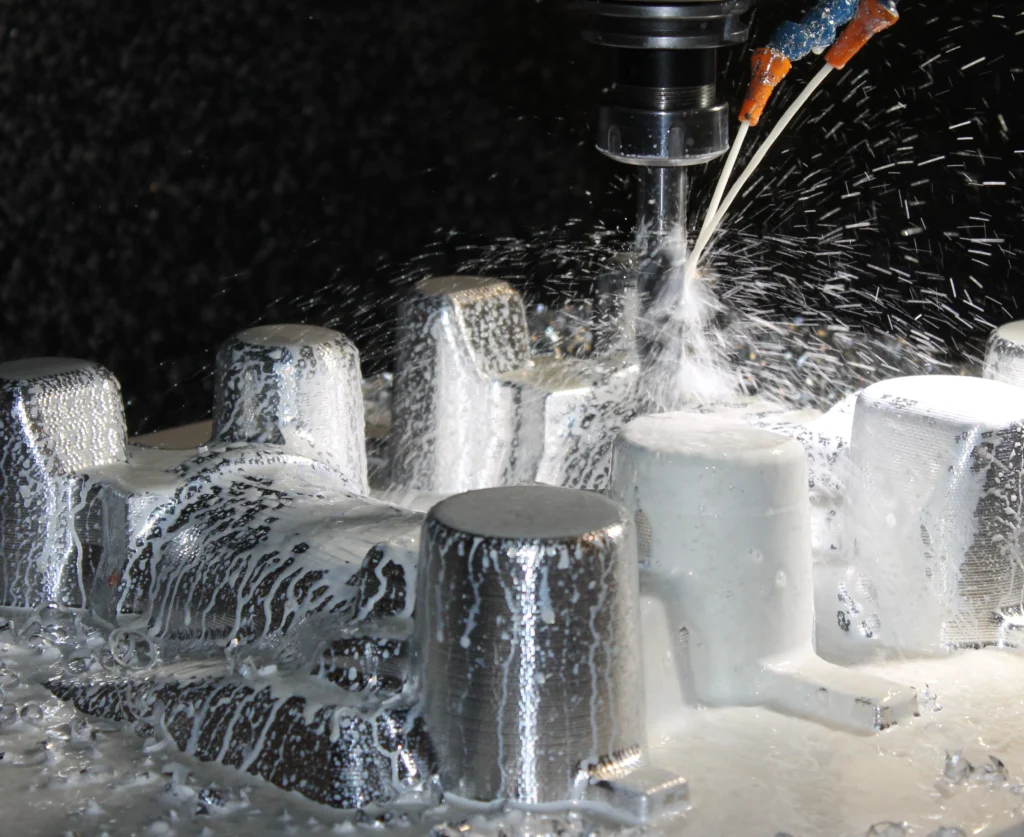
A fully integrated brass and bronze castings foundry
In over a century of casting corrosion-resistant parts, we’ve learned how to cast with a strength that meets conditions head on. In house, we can also offer aluminum casting and services like precision machining for better quality control and streamlined lead and delivery timelines.
Bronze and brass casting for better outcomes
Bronze and brass casting foundries capable of casting the world’s most complex components can be challenging to find. Since 1909, WAF has used proprietary processes to reliably deliver metal casting parts that hold up in harsh environments.
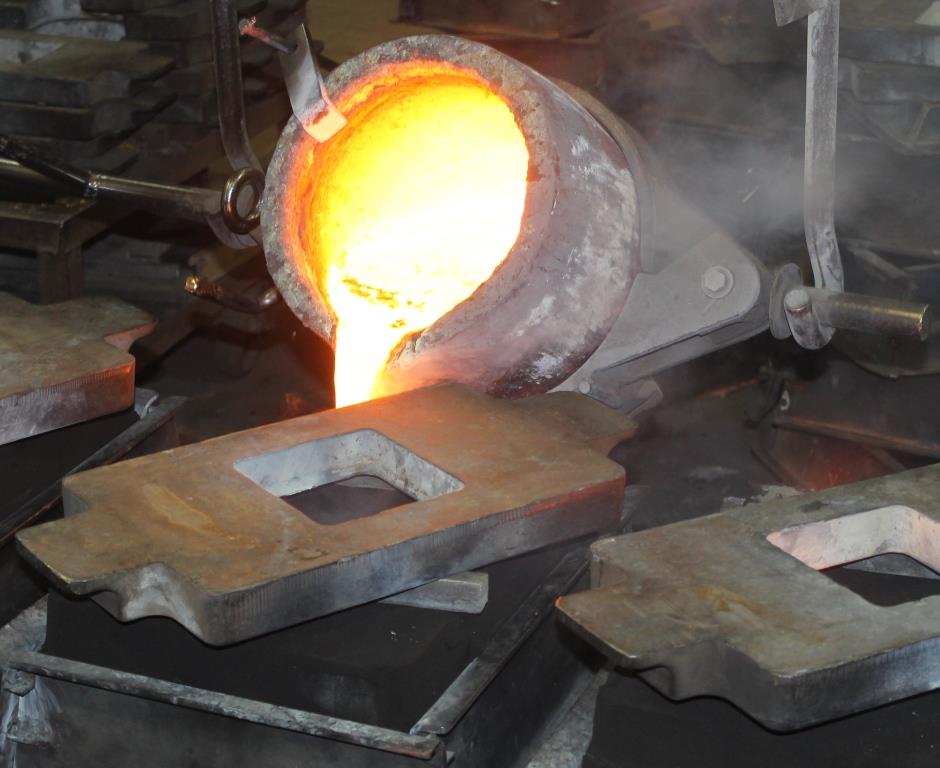
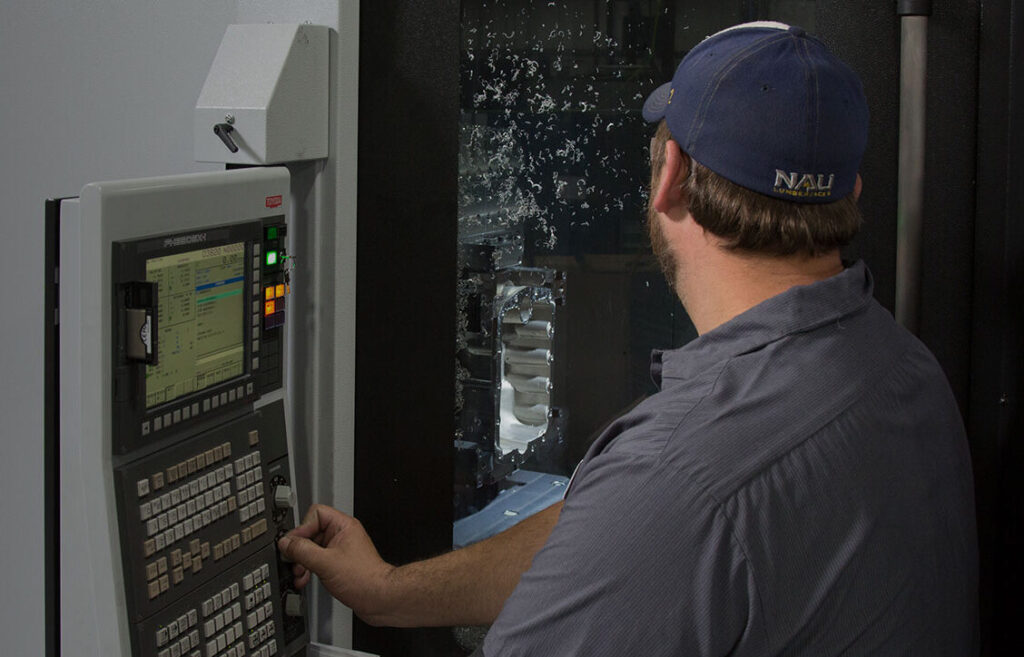
More In-house capabilities
In addition to bronze and brass, we offer aluminum casting across a range of volumes and sizes. WAF’s value-added services include in-house precision machining for better control and results on every cast.
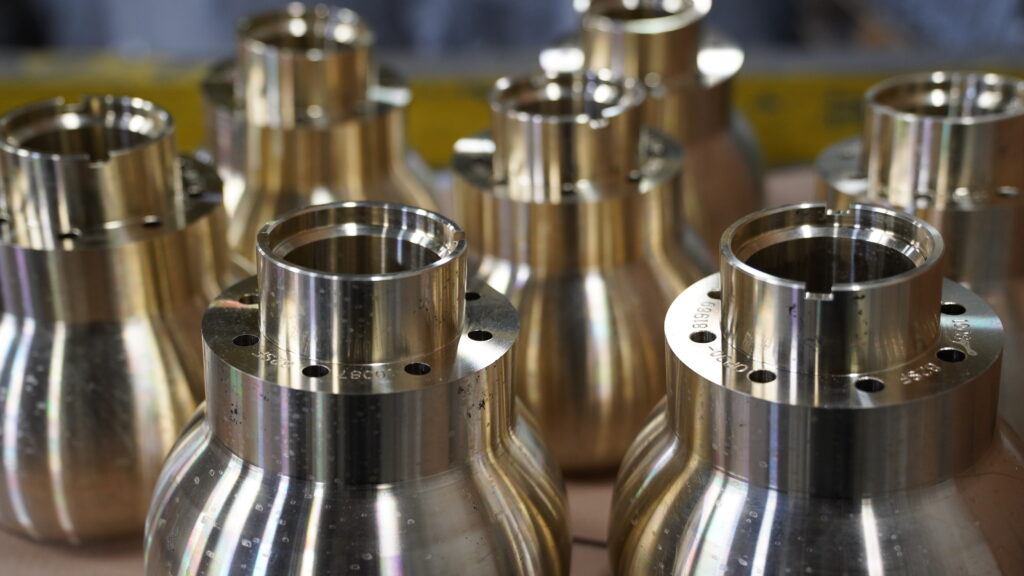
Reliable corrosion resistance
Brass and bronze is a highly specialized process, requiring a top-tier induction melter and the engineering know-how to melt, mold and cast to corrosion-resistant standards that your parts require.
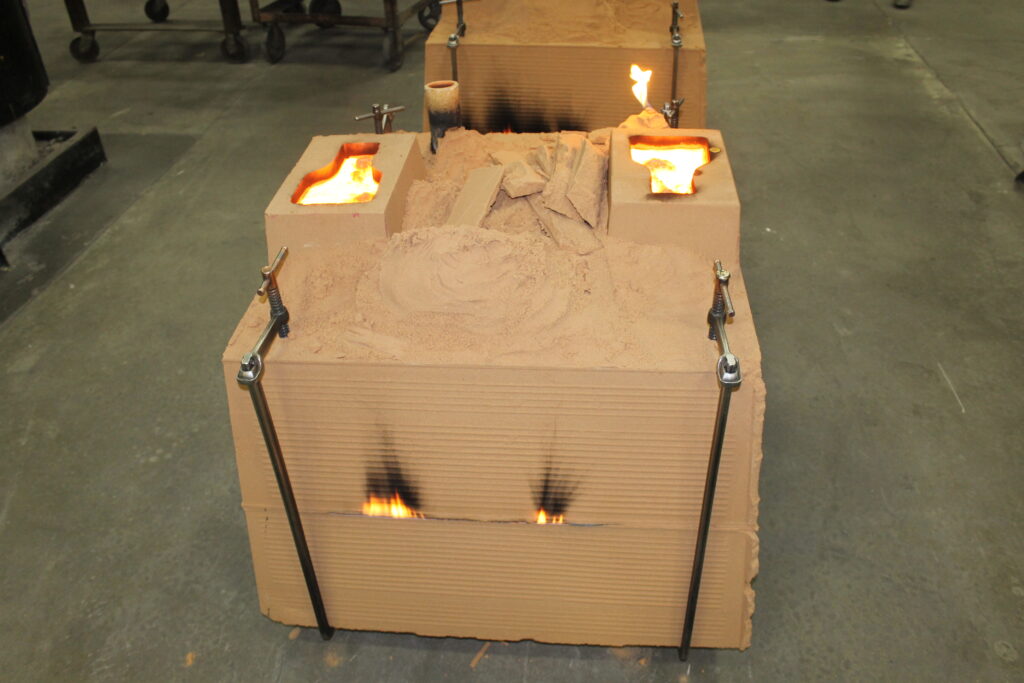
Experts in complexity
The word “no” is rarely in our vocabulary. That’s because our team of engineers excels at finding a way to bring even complex brass and bronze castings to production. Bring your challenge. WAF stands ready to solve it.
Your brass and bronze foundry, pouring what’s possible
From simple to complex, see how we can meet your requirements in brass and bronze casting.